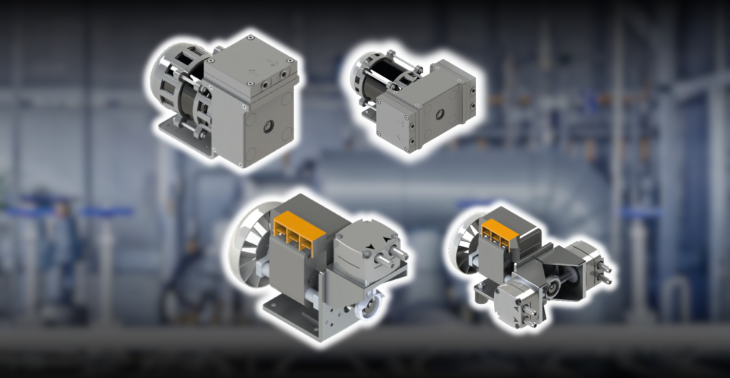
Sprężarka membranowa – budowa, działanie i zastosowanie
Sprężarki membranowe to zaawansowane technologicznie urządzenia, które dzięki swojej unikalnej konstrukcji znajdują szerokie zastosowanie w przemyśle i nauce. Ich hermetyczność, brak oleju w procesie sprężania oraz zdolność do pracy w trudnych warunkach czynią je niezastąpionymi w wielu specyficznych aplikacjach. W artykule omówimy budowę sprężarek membranowych, ich zasadę działania oraz różnorodne zastosowania. Poruszymy również różnice między sprężarką a pompą membranową, kwestie ciśnienia roboczego, zalety, opinie użytkowników oraz serwisowanie tych urządzeń.
Budowa sprężarki membranowej
Centralnym elementem sprężarki membranowej jest elastyczna membrana, zwana przeponą, wykonana z materiałów takich jak guma, silikon lub tworzywa odporne chemicznie, np. PTFE (teflon), w zależności od sprężanego medium. Membrana oddziela komorę sprężania od mechanizmu napędowego, eliminując kontakt gazu z olejem i innymi zanieczyszczeniami.
Mechanizm napędowy może być mechaniczny (np. wał korbowy z tłokiem) lub hydrauliczny, gdzie membranę porusza ciecz pod ciśnieniem. W modelach mechanicznych tłok zmienia objętość komory sprężania, a w hydraulicznych ciecz umożliwia uzyskanie wyższych ciśnień. Obudowa, zwykle wykonana ze stali nierdzewnej, zapewnia odporność na korozję, a zawory wlotowe i wylotowe kontrolują jednostronny przepływ gazu, zapobiegając jego cofaniu się.
Zasada działania
Zasada działania sprężarki membranowej opiera się na cyklicznym ruchu membrany, który zmienia ciśnienie w komorze sprężania. Podczas ruchu w dół membrana zwiększa objętość komory, obniżając ciśnienie i zasysając gaz przez zawór wlotowy. Następnie ruch w górę zmniejsza objętość, zwiększa ciśnienie i wypycha sprężony gaz przez zawór wylotowy.
Hermetyczna konstrukcja i brak kontaktu medium z elementami napędowymi są kluczowe w aplikacjach wymagających wysokiej czystości gazu. Warianty hydrauliczne dodatkowo umożliwiają uzyskanie bardzo wysokich ciśnień, co zwiększa ich wszechstronność.
Zastosowanie sprężarek membranowych
Sprężarki membranowe znajdują zastosowanie w wielu sektorach przemysłu i nauki. Poniżej przedstawiamy najważniejsze obszary ich wykorzystania.
Przemysł chemiczny i petrochemiczny
W tych branżach sprężarki membranowe sprężają substancje takie jak wodór, tlen czy gazy toksyczne. Ich hermetyczność minimalizuje ryzyko wycieków, a odporność na korozję umożliwia pracę z agresywnymi mediami.
Przemysł farmaceutyczny i biotechnologiczny
W farmacji i biotechnologii kluczowa jest wysoka czystość sprężonego gazu. Sprężarki membranowe bezolejowe eliminują zanieczyszczenia olejowe, jednak samo wyeliminowanie oleju nie gwarantuje sterylności wymaganej w produkcji leków czy szczepionek. W takich przypadkach stosuje się dodatkowe systemy oczyszczania, takie jak filtry, adsorbery czy sterylizacja UV, aby spełnić rygorystyczne normy.
Przemysł spożywczy
W produkcji żywności sprężone powietrze napędza maszyny, pakuje produkty i transportuje składniki. Sprężarki membranowe dostarczają gaz wolny od oleju, ale dla pełnej zgodności z wymogami sanitarnymi często stosuje się dodatkowe filtry.
Medycyna i technika laboratoryjna
W szpitalach i laboratoriach sprężarki membranowe dostarczają gaz do respiratorów, analizatorów oraz procesów badawczych. Są cenione za cichą pracę i niezawodność.
Energetyka i motoryzacja
W energetyce sprężarki wspierają instalacje wodorowe i turbiny. W motoryzacji znajdują zastosowanie w systemach wodorowych, analizatorach emisji spalin oraz precyzyjnych układach dozujących gazy. W typowych zadaniach, takich jak malowanie natryskowe, wciąż dominują jednak sprężarki tłokowe.
Pompa membranowa a sprężarka membranowa
Pompa membranowa i sprężarka membranowa różnią się przeznaczeniem oraz medium roboczym. Pompa membranowa przetłacza ciecze, w tym lepkie i zawierające cząstki stałe, co sprawia, że jest szeroko stosowana w przemyśle chemicznym, farmaceutycznym oraz w oczyszczalniach ścieków. Sprężarka membranowa natomiast spręża gazy, zwiększając ich ciśnienie do zastosowań przemysłowych, laboratoryjnych i magazynowania.
Ciśnienie robocze sprężarek membranowych
Ciśnienie robocze sprężarek membranowych zależy od ich konstrukcji i przeznaczenia:
- Małe modele (np. do aerografów) działają w zakresie 15–100 PSI.
- Średniej wielkości jednostki przemysłowe osiągają kilkaset PSI.
- Zaawansowane sprężarki hydrauliczne mogą przekraczać 6000 PSI.
- Mechaniczne sprężarki membranowe (niehydrauliczne) generują ciśnienia rzędu 3000–5000 PSI, co czyni je odpowiednimi do wymagających zastosowań, np. w przemyśle petrochemicznym.
Zalety sprężarek membranowych
Sprężarki membranowe oferują liczne korzyści:
✅Bezolejowość – Brak oleju w procesie sprężania zapewnia czysty gaz, choć w niektórych zastosowaniach konieczne są dodatkowe systemy filtracji.
✅Hermetyczność – Całkowicie zamknięta konstrukcja zapobiega wyciekom, co jest kluczowe przy pracy z toksycznymi i łatwopalnymi gazami.
✅Cicha praca – W porównaniu do sprężarek tłokowych generują mniej hałasu.
✅Niskie koszty eksploatacji – Prosta budowa zmniejsza ryzyko awarii, choć membrana jest elementem eksploatacyjnym i wymaga okresowej wymiany. Niektóre modele oferują membrany o wydłużonej żywotności, co obniża koszty serwisowe.
Opinie użytkowników o sprężarkach membranowych
Opinie użytkowników na temat sprężarek membranowych są zazwyczaj pozytywne. Użytkownicy cenią je za niezawodność, cichą pracę i wysoką czystość sprężanego gazu. Główne wady to konieczność okresowej wymiany membrany oraz wyższy koszt zakupu w porównaniu do tradycyjnych sprężarek tłokowych, co może stanowić barierę dla mniejszych firm.
Serwis i konserwacja sprężarek membranowych
Regularna konserwacja sprężarek membranowych obejmuje:
🔹 Wymianę membrany,
🔹 Kontrolę i czyszczenie zaworów,
🔹 Inspekcję uszczelnień i obudowy.
Modele z membranami o wydłużonej żywotności zmniejszają częstotliwość serwisowania.
Podsumowanie
Sprężarka membranowa to wydajne i wszechstronne urządzenie, łączące hermetyczność, bezolejowość i niezawodność. Wymaga regularnego serwisowania oraz dodatkowych systemów oczyszczania do uzyskania najwyższej czystości gazu. Dzięki szerokiemu zakresowi ciśnień roboczych oraz dostępności zaawansowanych modeli sprawdza się w przemyśle chemicznym, farmaceutycznym, spożywczym i motoryzacyjnym, a także w laboratoriach i energetyce.